Biaxially Oriented Polypropylene (BOPP) bags have revolutionized the packaging industry with their durability, versatility, and superior printability. They are widely used in sectors like agriculture, food, pet supplies, and more due to their ability to protect products while showcasing vibrant designs. Understanding how BOPP bags are made offers insight into why they are so popular and how manufacturers ensure consistent quality. This blog explores the step-by-step manufacturing process behind BOPP bags, detailing the techniques and technology that contribute to their exceptional performance.
What Are BOPP Bags?
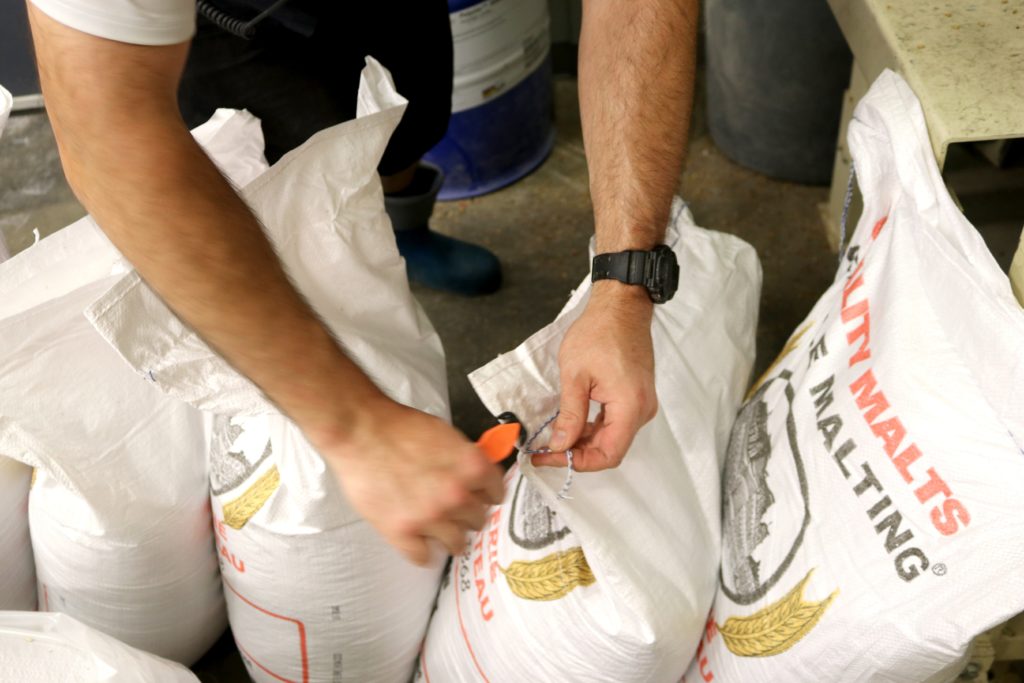
BOPP bags are made from polypropylene, a thermoplastic polymer known for its strength and flexibility. The term “biaxially oriented” refers to the stretching of polypropylene film in two perpendicular directions during production, which enhances its mechanical properties and clarity. This process creates a durable, lightweight material with excellent resistance to tearing, moisture, and chemicals. The bags are typically laminated and printed, making them ideal for high-quality branding and packaging.
Step 1: Raw Material Preparation
The manufacturing process begins with the procurement of raw materials, primarily polypropylene granules or pellets. These pellets serve as the base material for creating the film. Manufacturers often add specific additives to the polymer mix to enhance properties such as UV resistance, gloss, or printability.
The polypropylene granules are melted in an extruder, where they are subjected to high temperatures and pressure. This transforms the solid granules into a molten state, making them ready for film production.
Step 2: Film Extrusion
The molten polypropylene is extruded into a thin sheet or tube-like structure using a specialized die. This step forms the base film that will later be stretched to achieve biaxial orientation. Depending on the manufacturing setup, the extrusion process may produce a tubular or flat film.
In tubular extrusion, the molten polymer is extruded in the form of a bubble, which is then expanded and cooled. In flat film extrusion, the material is extruded as a flat sheet and transported through rollers for cooling and further processing.
Step 3: Biaxial Orientation
The defining feature of BOPP bags is the biaxial orientation of the polypropylene film. This involves stretching the film in two perpendicular directions—longitudinally (machine direction) and laterally (transverse direction). This process enhances the film’s strength, flexibility, and clarity.
- Longitudinal Stretching: The film is first stretched in the machine direction using rollers that move at varying speeds. This aligns the polymer molecules along the film’s length, improving its tensile strength.
- Lateral Stretching: After longitudinal stretching, the film is heated and stretched in the transverse direction using a tenter frame. This process aligns the polymer molecules across the width of the film, further enhancing its mechanical properties.
The result is a biaxially oriented film with superior strength, clarity, and barrier properties.
Step 4: Surface Treatment
To prepare the film for printing and lamination, it undergoes a surface treatment process, typically corona or plasma treatment. These techniques increase the film’s surface energy, improving adhesion for inks and adhesives.
- Corona Treatment: The film is exposed to a high-frequency electrical discharge, which alters its surface properties and makes it more receptive to printing.
- Plasma Treatment: This involves exposing the film to a plasma field, achieving similar effects with greater precision and uniformity.
Surface treatment is essential for ensuring high-quality printing and durable lamination.
Step 5: Printing
BOPP bags are known for their vibrant and high-quality prints, which play a crucial role in branding and consumer appeal. The printing process typically uses advanced techniques such as flexographic or gravure printing.
- Flexographic Printing: This method uses flexible relief plates to transfer ink onto the film. It is ideal for high-speed printing and produces sharp, vibrant designs.
- Gravure Printing: In this technique, ink is applied using engraved cylinders. Gravure printing offers excellent precision and is preferred for intricate designs and high-volume production.
Manufacturers use specialized inks that adhere well to the treated film, ensuring long-lasting and smudge-free prints.
Step 6: Lamination
Lamination involves bonding the printed BOPP film to another layer of material, such as woven polypropylene fabric, to create a multi-layer structure. This process enhances the bag’s strength, durability, and moisture resistance.
- Adhesive Lamination: A layer of adhesive is applied between the BOPP film and the woven fabric, bonding them together under heat and pressure.
- Extrusion Lamination: In this method, a molten polymer layer is used as the bonding agent, providing a seamless and durable connection between layers.
The laminated structure combines the visual appeal of the BOPP film with the structural integrity of the woven fabric, resulting in a robust yet attractive packaging solution.
Step 7: Cutting and Stitching
Once the laminated material is ready, it is cut and stitched into the desired bag size and shape. Automated cutting machines ensure precision in dimensions, while stitching or heat-sealing secures the edges.
- Cutting: The laminated rolls are fed into cutting machines that trim them into specific sizes based on customer requirements.
- Stitching or Sealing: The edges are stitched using durable threads or heat-sealed for a seamless finish. Bottoms of the bags are often reinforced to handle heavy loads.
This step finalizes the physical structure of the BOPP bags, making them ready for use.
Step 8: Quality Inspection
Quality control is a critical part of the manufacturing process. Each batch of BOPP bags undergoes thorough inspection to ensure they meet industry standards and customer specifications. Factors like print quality, strength, size accuracy, and lamination integrity are evaluated during this stage.
Advanced testing equipment is often used to measure tensile strength, tear resistance, and moisture barrier properties. Only bags that pass all quality checks are approved for packaging and distribution.
Step 9: Packaging and Distribution
The finished BOPP bags are packed in bundles and prepared for shipping. Manufacturers often customize packaging to align with customer branding or logistical requirements. The bags are then distributed to industries such as agriculture, food processing, and retail, where they are used to package and protect products.
Conclusion
The manufacturing process of BOPP bags is a blend of precision, technology, and innovation. From raw material preparation to lamination and quality inspection, each step contributes to creating a product that combines functionality with aesthetic appeal. BOPP bags have become a cornerstone of modern packaging, offering durability, versatility, and excellent branding opportunities. Understanding their manufacturing process highlights the effort and expertise involved in delivering this high-performance packaging solution, ensuring it meets the diverse needs of industries worldwide.